Liburdi Laser Systems
GreenEco is a representative of the Liburdi group, a world known authority in the field laser materials processing. Liburdi’s engineers are the world known experts in the field of materials science and materials engineering, welding processes, laser materials processing, system integration and software development for the highest quality automated welding systems.
For more information, please visit our partners website at:
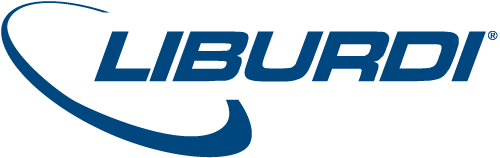
Liburdi
Liburdi Automation is an industry leader in the development of automated welding systems for turbine, aerospace and manufacturing applications. Liburdi has extensive knowledge of metallurgy, engineering, robotics and controls, and other related fields. All Liburdi automated welding systems can be adapted to specific requirements. The LAWS™ automatic welding system from Liburdi is an industry standard for welding of turbine and compressor blades, while Dabber® welding machines are widely used for the seal and rotor applications.
Liburdi Pulsweld® precision power sources are known for its accuracy and repeatability, with proven performance in the aerospace, nuclear, medical, automotive, pipe factories and B&R projects. Pulsweld® power sources are available in both GTAW and PAW configurations, and together with patented variable polarity systems are technologies that are selected for critical aviation welding applications, such as for example, the space launch vehicles.
LAWS1000 systems
Typical applications of automated welding systems – LAWS 1000 with integrated robot, welding unit and vision system are used for welding of:
Łopatki sprężarkowe LPC, IPC i HPC
Rotors of compressors, BLISK / IBR (integrated impeller rotors)
HPT, IPT and LPT turbine blades
The LAWS1000 model of the suspended crane with 3-6 axes is able to accommodate many devices.
Three-dimensional imaging and image processing Liburdi Vision System ™ (LVS) is responsible for the weld path and welding parameters. LVS is fully integrated with the computer-based Liburdi Robotic Controller ™ (LRC), providing for real-time monitoring during the welding process.
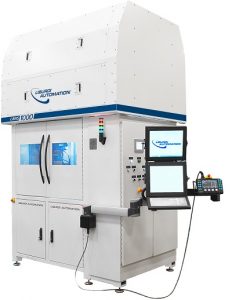
System configuration options:
- YAG, fiber laser power supply technology
- LAWS 1000 frame and architecture with Class 1 enclosure
- Arm and controller
- Pneumatic rupture protection
- Work envelope 18 “(46 cm) x 32” (81 cm) x 12 “(30 cm)
- A typical size of parts 24 “(60 cm) x 12” (30 cm)
- LENS tracking system
- Powder mass flow controller
- Optional wire feeding
- Recirculated powder container
We also offer the option of Liburdi “turnkey” systems, which include the development of the welding process, NDT testing, metallurgical certification, training and commissioning, with various configurations for a variety of applications in aviation and power industry, including HPT blades, shielded LPT blades, blades and compressor seals.