Applications - Power generation
The extreme conditions in which equipment and structures in the power generation industry operate, require the use of special protective materials that will significantly extend their operational life under optimal conditions.
Unprotected components are exposed to high-temperature corrosion, erosion and slagging, which cause frequent, often unpredictable catastrophic equipment failures, resulting in extended downtime, increased maintenance costs, reduced equipment’s efficiency and lower production volumes.
Depending on the individual problem and operational requirements, we can offer an effective solution, optimized for the application specifics.
Our GreenEco ceramic coatings as well as the metallic TuffStuff and TuffCorr coatings have been specially developed with a single goal – to effectively protect boiler tubes against the erosion, corrosion and slagging, regardless of the fuel type ( coal, lignite, biomass, waste products).
- Our unique, advanced amorphous metal coating, Tuff-888, guarantees the highest available protection for boiler tubes operating in the toughest operating conditions, one that is absolutely not achievable by the competition.
- Ceramic coatings provide effective long term protection for the boiler tube surface against high-temperature chemical corrosion, and slagging.
- The latest generation of GreenCoat-HE emission coatings have been developed to significantly increase the efficiency of gas fired heating systems, resulting in production’s cost reduction, increased production volumes and reduced emission.
- Thermally insulating nano-ceramic coatings from the TC-100 group allow for a significant reduction in the surface temperature of industrial equipment and buildings (tanks, fittings, pipelines, roofs and others) while reducing energy losses. The use of these coatings allows for a reduction of energy losses by about 10% - 15%).
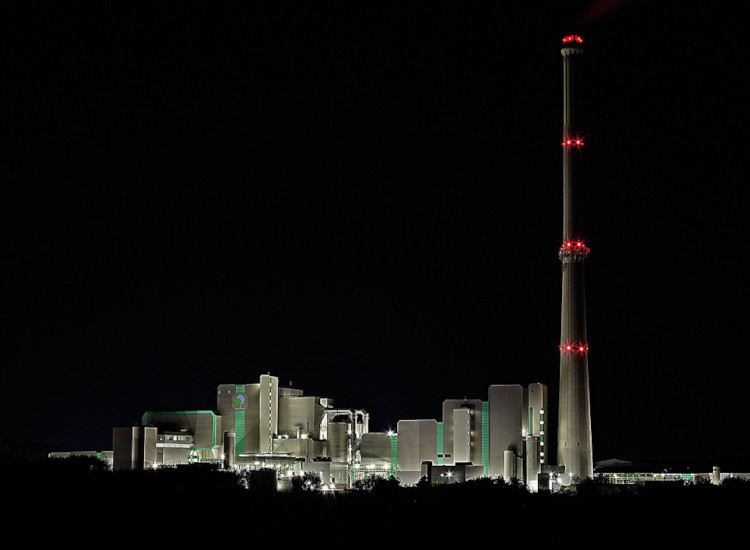
The GreenEco offers you the latest innovative solutions to increase the efficiency of technological processes and thus ensure significant savings related to reduced gas fuel consumption, corrosion and erosion related equipment damage and reduction of CO2 emissions.
The less energy absorbed by the refractory lining, the more efficient the system is. Greater efficiency means faster heating (reduced cycle time), which in turn results in a significant cost reduction. Typical savings for the natural gas and oil sectors resulting from the application of the GreenCoat-HE, high emissivity coatings on average is within the 3% up to 10% range.
Application of our high-emissivity nano-ceramic layers in large industrial heating systems not only effectively protect the surfaces of pipes and refractory linings against high-temperature degradation, but also significantly improves the efficiency of equipment and increases the efficiency of production processes.
GreenCoat-HE coating systems are ceramic materials with high emissivity and re-emissivity of thermal radiation, specially developed for gas-fired industrial heaters, operating in temperatures up to 1650 °C. Application of the GreenCoat-HE coatings results in improved heat transfer, energy savings, increased production, reduced downtime, increased equipment lifetime (tubes and refractories) and indirectly reduces harmful emission.
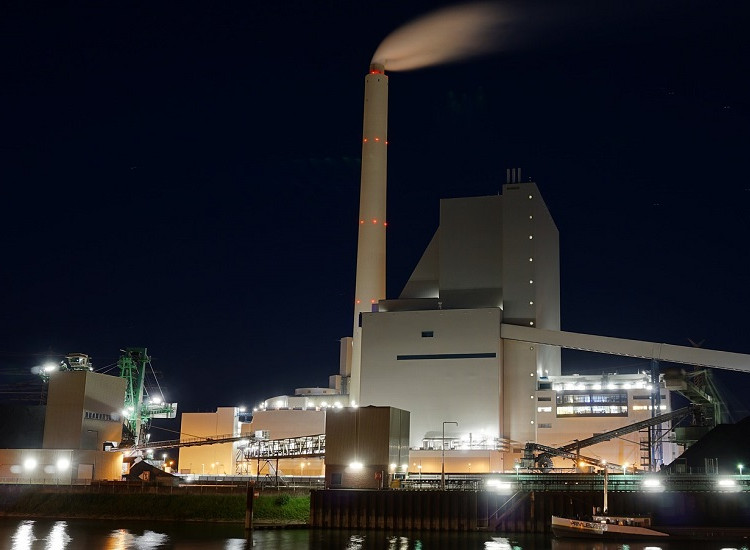
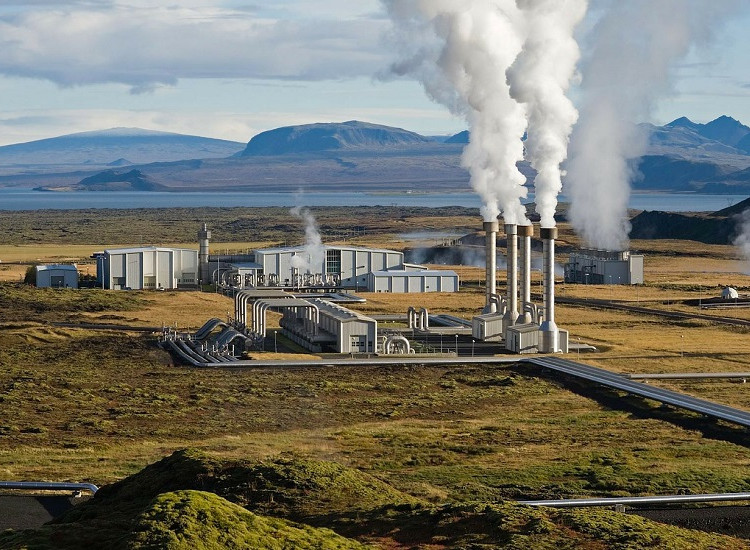
The most important features of GreenCoat-HE include:
- Operational temperatures up to 1650 ° C
- High resistance to thermal shocks
- High chemical corrosion resistance
- Adhesion - bond strength over 350 bar
- Typical thicknesses, depending on conditions - 50 - 100 μm
- The emissivity in the range of 0.85 - 0.95 (for comparison, typical refractory materials have an emissivity of 0.4 – 0.6)
Typical Applications
GreenEco and GreenCoat-HE ceramic coatings offer proven solutions to serious problems in power plant boilers and industrial systems. Typical applications for our materials include:
- Boiler walls and boiler tube protection
- Superheaters
- Heat exchangers
- Boilers and furnaces - refractory materials
- Exhaust gas systems
- Chimneys
- Heaters
- Sealer for metallic coatings
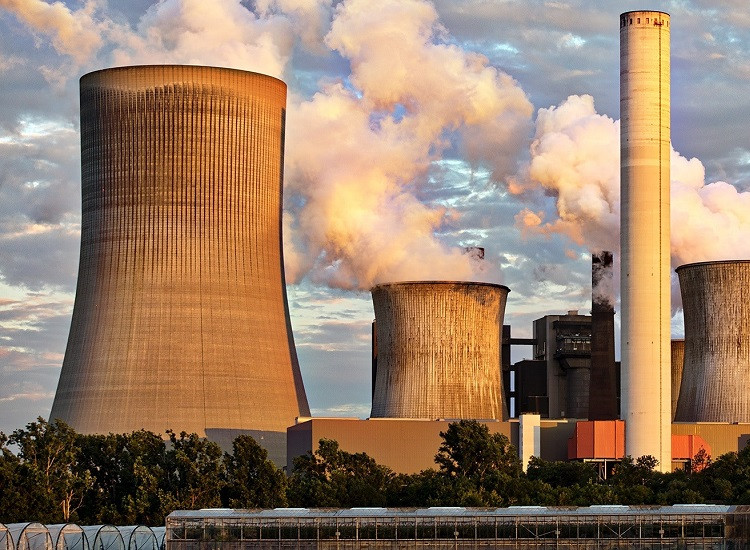
Features and Benefits
We offer proven solutions, which have been designed to work in extreme temperatures, corrosive atmospheres, erosion conditions and heave slagging. The properly selected materials are applied on specially prepared metallic and/ or refractory surface, creating a monolithic defect free barrier that will work in the most difficult operating conditions, typical for boilers and industrial heaters.
Benefits:
- Lower maintenance costs
- Reduces repairs and downtimes
- Higher efficiency
- Extends the life of equipment
- Protects against abrasion, impacts and slagging
- Provides very effective corrosion protection
- The material adheres to almost any surface, regardless of shape and size
- The material works together with the substrate, taking into account the thermal expansion of the substrate
- Can operate at the very high temperatures